Preventing Electrocution in the Workplace: Tips and Best Practices
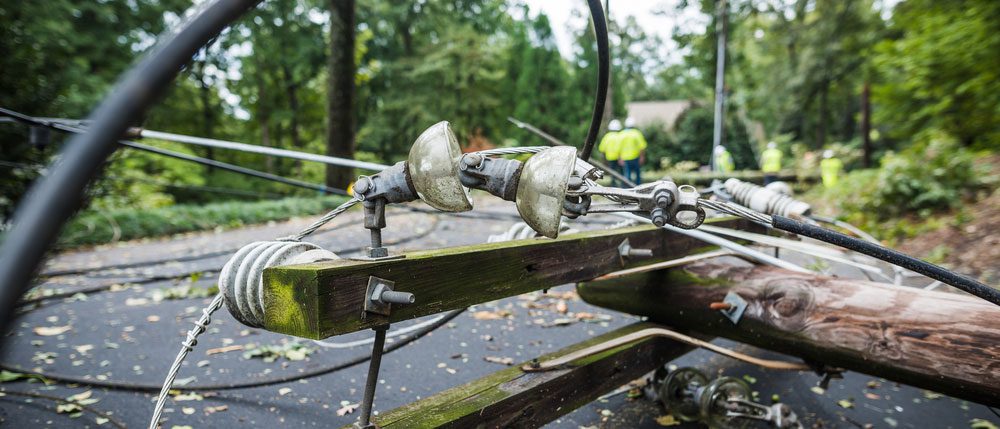
What is Electrocution in the Workplace?
Electrocution in the workplace occurs when a person comes into direct or indirect contact with an electrical source, resulting in a sudden and harmful flow of electric current through the body. This can lead to severe injuries, tissue damage, burns, or even fatality, depending on the voltage and duration of exposure. Common causes of workplace electrocution include faulty wiring, improperly maintained equipment, lack of proper grounding, and insufficient safety training. Understanding these hazards is critical for implementing effective safety measures and ensuring a safe working environment for all employees.
Preventative Measures
To protect employees from the dangers of electrocution in the workplace, it’s essential to establish robust safety protocols. Regular equipment inspections and maintenance, proper grounding of electrical systems, and comprehensive safety training for all staff are fundamental steps. Employers should also ensure that all electrical work is conducted by qualified professionals and that safety signs are displayed in areas with high electrical risks.
For more information and legal assistance regarding workplace electrocution injuries, visit Philadelphia electrocution injury lawyers.
Electrocution vs Shock
While both electrocution and electric shock involve exposure to electrical current, they differ significantly in their outcomes. An electric shock occurs when electrical energy flows through a person’s body, causing involuntary muscle contractions and varying degrees of discomfort or pain. Electric shocks can range from mild, momentary tingles to severe, prolonged jolts that cause significant injury but are not necessarily fatal. In contrast, electrocution specifically refers to a fatal exposure to electrical current. Essentially, all electrocutions cause electric shock, but not all electric shocks result in electrocution.
Common Workplace Scenarios Leading to Electrocution
Understanding typical scenarios that can lead to electrocution is essential for prevention. Common situations include:
- Wet Environments: Working in damp or wet conditions without proper insulation can significantly increase the risk of electrocution.
- Faulty Equipment: The use of worn-out, damaged, or improperly maintained electrical tools and machinery.
- Overhead Power Lines: Contact with overhead electrical lines, commonly encountered in construction and outdoor maintenance activities.
- Lack of Grounding: Working with electrical systems that are not properly grounded, leading to increased danger.
- Inadequate Training: Employees not receiving adequate training and education on electrical safety protocols.
Best Practices for Preventing Electrocution in the Workplace
Best Practices for Preventing Electrocution in the Workplace
- Conduct Regular Inspections: Regularly inspect all electrical equipment, wiring, and systems for signs of wear and tear, damage, or faulty installation. Promptly address any identified issues to prevent potential hazards.
- Use Personal Protective Equipment (PPE): Ensure that employees are equipped with appropriate PPE, such as insulated gloves, safety boots, and protective clothing, when working with or around electrical systems.
- Implement Lockout/Tagout Procedures: Establish and enforce lockout/tagout (LOTO) procedures to ensure that electrical systems are de-energized and locked out during maintenance or repair work, preventing accidental re-energization.
- Provide Comprehensive Training: Offer thorough and ongoing training on electrical safety to all employees, including the proper use of equipment, emergency response procedures, and the importance of adhering to safety guidelines.
- Ensure Proper Grounding: Verify that all electrical systems and equipment are properly grounded to reduce the risk of electrocution. Grounding provides a safe path for electrical current to follow in the event of a fault.
- Maintain a Dry Workspace: Keep work areas dry and free from moisture. Use insulation mats and other protective measures when working in or near wet environments to minimize the risk of electrical accidents.
- Use Ground Fault Circuit Interrupters (GFCIs): Install GFCIs in areas with high exposure to moisture or where portable electric tools are used. GFCIs can quickly shut off the power in the event of a ground fault, protecting individuals from electric shock.
By incorporating these best practices, employers can create a safer workplace and significantly reduce the risk of electrocution. Promoting a culture of safety and vigilance is key to preventing electrical accidents and ensuring the well-being of all employees.
Tips to Prevent Electrocution in the Workplace
Important Safety Tips to Follow
Prevention is the cornerstone of safety when it comes to electrical hazards in the workplace. Here are additional safety tips to further mitigate the risk of electrocution:
- Identify Electrical Hazards: Regularly survey the workplace for potential electrical hazards and make note of any risks. Ensure that all hazards are clearly marked with appropriate warning signs.
- Proper Use of Extension Cords: Avoid using extension cords as a permanent solution for providing power. If needed, use heavy-duty, industrial-grade extension cords and never daisy-chain multiple cords together.
- Circuit Breaker Panels: Ensure that all circuit breaker panels are easily accessible, clearly labeled, and regularly maintained. Know where the main breakers are located in case of an emergency shut-off.
- Avoid Overloading Circuits: Prevent overloading electrical circuits by distributing the electrical load evenly. Use power strips with built-in circuit breakers to help protect against overload.
- Stay Informed: Keep up to date with the latest standards and regulations for electrical safety, such as those published by the Occupational Safety and Health Administration (OSHA) and the National Fire Protection Association (NFPA).
- Emergency Preparedness: Develop and practice emergency response plans in case of an electrical accident. This includes having first aid kits readily available and ensuring that employees are trained in cardiopulmonary resuscitation (CPR) and first aid.
Best Practices for Electrical Safety
Best Practices for Electrical Safety in Specific Work Environments
Different work environments present unique challenges and risks when it comes to electrical safety. Here are tailored best practices for various settings:
Construction Sites
- Vehicle and Machinery Safety: Ensure that all heavy machinery and construction vehicles are regularly inspected and maintained. Electrical components such as wiring and connectors should be checked frequently for damage.
- Scaffold and Ladder Use: When using scaffolding and ladders near electrical installations, maintain a safe distance and use non-conductive materials to prevent accidental contact with live wires.
- Temporary Power Supplies: Use ground fault circuit interrupters (GFCIs) with temporary power supplies and generators to protect against electrical faults. Ensure that all temporary setups are installed by qualified professionals.
- Awareness and Coordination: Maintain clear communication and coordination between all workers on-site, especially when working near live electrical systems. Use radios or hand signals to stay informed of ongoing work.
Industrial Facilities
- High-Voltage Equipment: Only authorized and trained personnel should operate or service high-voltage equipment. Follow strict lockout/tagout (LOTO) procedures to prevent accidental energization.
Machine Guarding: Ensure that all machinery with electrical components is equipped with appropriate guards and safety interlocks to prevent accidental contact with moving parts or live wires.
- Control Panels and Switchboards: Keep control panels and switchboards locked and accessible only to qualified individuals. Regularly inspect and label all electrical panels to mitigate risks.
- Routine Audits: Conduct frequent safety audits to identify and address potential electrical hazards. Use audit findings to implement continuous improvements in safety protocols.
Office Environments
- Workspace Setup: Arrange workstations to minimize the risk of tripping over cables and power cords. Use cable management systems to keep cords organized and out of the way.
- Portable Devices: Ensure that portable devices and chargers are in good condition and used in compliance with manufacturer guidelines. Avoid overloading power outlets.
- Regular Maintenance: Schedule routine maintenance for all office electrical systems, including lighting, HVAC controls, and computer networks. Ensure that maintenance is conducted by certified electricians.
- Employee Training: Provide training for office staff on the basics of electrical safety, including how to identify faulty equipment and the steps to take during an electrical emergency.
By tailoring best practices to specific environments, employers can more effectively mitigate the risks associated with electrical hazards, ensuring a safer workplace for all employees. Continuously reviewing and updating safety protocols is essential to keeping up with advancements in technology and changes in workplace dynamics.
Reporting and Responding to Electrical Incidents
Effective reporting and response protocols are crucial for handling electrical incidents. Implementing a clear procedure for reporting hazards and incidents can significantly reduce the impact of such events. Here are steps to follow:
- Immediate Reporting: Encourage employees to immediately report any signs of electrical hazards, such as sparks, burning smells, or unusual noises. Provide multiple channels for reporting, such as through a safety app or dedicated hotline.
- Incident Investigation: Upon receiving a report, conduct a thorough investigation to identify the root cause of the incident. Involve safety officers, electricians, and relevant personnel in the investigation process.
- Corrective Actions: Develop and implement corrective actions based on investigation findings. These may include repairing or replacing faulty equipment, updating safety protocols, or providing additional training.
- Documentation: Maintain detailed records of all incidents, investigations, and corrective actions. Use this data to identify patterns and areas for improvement in your electrical safety program.
Employee Support: Offer support to employees affected by electrical incidents. This may include medical assistance, counseling, and ensuring a safe return to work.
By following these guidelines, organizations can foster a proactive approach to electrical safety, reducing the likelihood of incidents and ensuring swift and effective responses when they do occur.
FAQs About Preventing Electrocution in the Workplace
How can employees avoid electrical hazards?
Employees can avoid electrical hazards by adhering to the following safety practices:
Use PPE
- : Always wear appropriate personal protective equipment (PPE) such as insulated gloves, safety goggles, and rubber-soled shoes when working near electrical sources.
- Never Tamper with Equipment: Do not attempt to repair or tamper with electrical equipment unless you are qualified and authorized to do so. Always wait for a certified electrician to handle electrical issues.
Stay Informed
- : Attend all safety training sessions provided by your employer and stay current on best practices for electrical safety.
- Report Hazards: Immediately report any damaged or malfunctioning electrical equipment to your supervisor or safety officer.
What should you do in case of an electrical shock?
In the event of an electrical shock:
- Do Not Touch: Do not touch the person being shocked with your bare hands. Use a non-conductive object to push them away from the electrical source.
- Disconnect Power: If possible, safely disconnect the power source using a circuit breaker or switch.
Call for Help
- : Dial emergency services immediately and provide clear, concise information about the incident.
- Administer First Aid: If it’s safe to do so, administer first aid or CPR if you are trained. Avoid moving the injured person unless they are in immediate danger.
Are regular inspections necessary?
Yes, regular inspections are crucial to maintaining electrical safety. Conduct the following inspections:
- Visual Inspections: Regularly perform visual inspections of electrical cords, outlets, and equipment for signs of wear, damage, or overheating.
- Professional Assessments: Schedule periodic inspections by qualified electricians to identify and rectify potential electrical issues that are not easily visible.
- Compliance Audits: Ensure that all electrical installations and regular maintenance activities comply with local and national electrical codes and regulations.
Ensure Workplace Safety: Implement Electrical Safety Best Practices
Adopting recommended safety practices can greatly reduce the risk of electrocution, creating a safer environment for all employees. Employers and employees must collaborate to foster a safe working environment by adhering to best practices, conducting regular training, and proactively identifying and mitigating potential hazards. Prioritize electrical safety to protect your workforce, enhance operational efficiency, and boost overall workplace morale.